Unveiling the effect of Ti substitutions on the static oxidation behavior of (Hf,Ti)C at 2500 ℃
Published 03 February, 2024
Hf-based carbides are highly desirable candidates for thermal protection applications above 2000 ℃ due to their extremely high melting point and favorable mechanical properties. However, as a crucial indicator for composition design and performance assessment, the static oxidation behavior of Hf-based carbides at their potential service temperatures has been rarely studied.
In a study published in the KeAi journal Advanced Powder Materials, a group of researchers from Central South University and China Academy of Launch Vehicle Technology revealed the static oxidation mechanism of (Hf, Ti)C bulks at 2500 ℃, as well as the effect of Ti substitutions on their oxidation behaviors.
"The addition of Ti element can make the microstructure of HfC oxide layer more complex,” explained Shiyan Chen, lead author of the study. “Typically, such a composite oxide layer has better protective properties.”
The thickness of the oxide layer on the surface of (Hf, Ti)C was reduced by 62.29 % compared with that on the HfC monocarbide surface after oxidation at 2500 ℃ for 2000 s. The dramatic improvement in oxidation resistance was attributed to the unique oxide layer structure consisting of various crystalline oxycarbides, HfO2 and carbon.
“The Ti-rich oxycarbide ((Ti, Hf)CxOy) dispersed within HfO2 formed the major structure of the oxide layer. A coherent boundary with lattice distortion existed at the HfO2 / (Ti, Hf)CxOy interface along the (111) crystal plane direction, which served as an effective oxygen diffusion barrier,” added Chen.
The Hf-rich oxycarbide ((Hf, Ti)CxOy) together with (Ti, Hf)CxOy, HfO2, and precipitated carbon constituted a dense transition layer, ensuring favorable bonding between the oxide layer and the matrix. Furthermore, the Ti content affects the diffusion of carbon in (Hf, Ti)C lattice and the distribution of Ti-rich oxycarbide, which will further determine the structural integrity of the oxide layer. Based on the results of oxidation kinetics, 30%-40 at. % Ti substitution provides the best enhancement of oxidation resistance.
According to Professor Zhaoke Chen, co-lead and corresponding author, this study represents a novel exploration in the field of ultra-high temperature ceramics (UHTCs). "Our study enhances the comprehension of the structural evolution during ultra-high temperature oxidation. The findings offer theoretical guidance for optimizing the composition of UHTCs to broaden their applications at ultra-high temperatures,” said Chen.
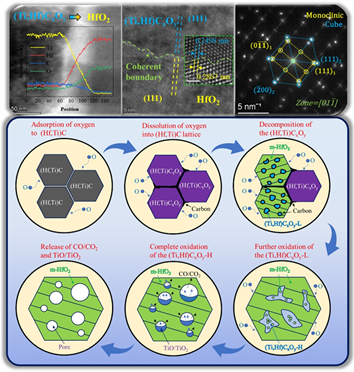
Image: Schematic diagram of (Hf, Ti)C oxidation mechanism
Contact author details: Zhaoke Chen and Xiang Xiong, State Key Laboratory of Powder Metallurgy, Central South University, Changsha 410083, China
chenzhaoke2008@csu.edu.cn (Zhaoke Chen)
xiongx@csu.edu.cn (Xiang Xiong)
Funder: This work was supported by the National Natural Science Foundation of China grant numbers [52072410].
Conflict of interest: The authors declare that they have no known competing financial interests or personal relationships that could have appeared to influence the work reported in this paper.
See the article: Chen, Shiyan, et al. "Insight into the effect of Ti substitutions on the static oxidation behavior of (Hf, Ti) C at 2500° C." Advanced Powder Materials 3.2 (2024): 100168.
https://doi.org/10.1016/j.apmate.2023.100168